
Capstone
Project 1: Two-way Slab Design
The purpose of the project is to design a two-way concrete slab and their supporting beams for the floor plan provided by an Architecture Firm. This construction project is for the renovation of a parking lot of Palomar Airport in Carlsbad, CA. The normal-weight concrete slab will be designed using codes in ASCE 7-16 and ACI 318-19. These codes will be used to determine factored loading conditions for the parking structure. Lateral Loading will not be considered for this case.
The procedures for designing the concrete slabs and supporting beams is the following: determine the minimum slab thickness, determine the factored loading conditions, determine the nominal moment and shear capacities, and select a reinforcement bar size and type. The loading calculations and the nominal moment and shear capacities will be determined by using the strip method and the yield line method.
The Design Brief
Dimensions & Section Properties
Minimum Two-Way Slab Depth
The minimum slab depth for the two-way slab was calculated by the following steps: calculating the minimum flange width for every girder in the structural system, calculating the gross moment of inertia for the girders and corresponding slabs, calculating the flexural the stiffness ratio , and verifying the initial slab width. ACI 318-19 Chapter 8 aided in the design and calculations of the two-way slab depth. These steps helped determine the minimum slab depth. The minimum slab depth for the two-way slab is: ℎ = 7".
Minimum One-Way Cantilever Slab Depth
The minimum slab depth for the on-way slab set as a cantilever slab was determine using ACI 318 Table 7.3.1.1. The minimum thickness of a solid one-way slabs is determined by 𝑙/10. The minimum slab thickness for the concrete on-way slab is: ℎ = 10". This will be the minimum for the entire slab to keep the slab thickness of the entire structural system consistent and continuous.
Columns
The column dimensions were given by the project architects and is measured to be a 30” x 30” square.
Girders
Similar to the dimensions of the columns, the girders are also designed as a 30” x 30” square. The clear lengths of the girders are the following: 𝑙𝑥 = 23’ − 0”; ly=18'-0”; 𝑙𝑐 = 5” − 6".
Clear Concrete Cover
Per ACI 318-19 Table 20.5.3.2 the minimum concrete cover will be 3”.
Design Loads for Slab
Self-Weight
The self-weight of the slab was given by the properties of normal-weight concrete having a unit weight of 𝛾 = 150 𝑝𝑐𝑓. Moreover, the compressive strength of concrete was given as 𝑓’𝑐 = 4100𝑝𝑠𝑖. The self-weight load was calculated by multiplying the unit weight of concrete and the thickness of the slab of 10”; this was calculated to be 𝑤o = 125𝑝𝑠𝑓.
Superimposed Dead Load
The Superimposed dead load was given as 18 psf. Moreover, there is a superimposed dead linear load that was given as 250plf.
Live Load
The live load was determined by ASCE 7-16 for a general parking structure as 40 psf. No live-load reduction is done to this live load as stated per ASCE 7-16.
Factored Load
The factored load was calculate using the following load combination of 𝑤u = 1.2D + 1.6L . Using the strip method, a unit length of 1ft was multiplied to the area load. The factored load per 1ft unit length is 𝑤u = 235.6 𝑙𝑏/𝑓𝑡. Similarly, 𝑃u = 300𝑙𝑏/𝑓𝑡.
Design Load for Girder
Self-Weight
The girder self-weight is calculated by taking the area of the girder under the slab and multiplying it by the unit weight of concrete. This is the taken area of the girder as the weight of the concrete slab above the girder is already considered, calculated, and factored in the loading out loading conditions. This gives the following solution: 𝑤o = 750 𝑙𝑏/𝑓𝑡.
Structural Analysis - Slab
Strip Method
Analysis of Strip Method
The strip method involved analyzing the structural loads of the slab and simplifies the loading conditions into a unit length; in this case the unit length is 1ft and three different strips were created and analyzed. This shows that the longest strip was divided into three different loading conditions and each with its own percentage of the original factored load 𝑤u. The longest strip consisted of 65%, 60% and 65% along the vertical direction of the beam. The other two loading conditions were taken as either point load, 100%, and 35% or point load, 100%, and 40% of the factored load along the horizontal directions. Structural-Analyzer.com was used to determine the maximum governing moment and shears; the analyzer provided shear and bending moment diagrams. The following figures show the bending moment and shear diagrams for all three strips.
Determining the Governing Shear and Bending Moments
The diagrams show the maximum positive and negative moment and maximum absolute shear. These values will be used to determine the required number of bars needed for the slab reinforcement; they will be used as the governing shear and bending moment capacities.
A table is then set up using an Excel spreadsheet to determine the nominal moment capacity for a #4 bar for different spacing; this Excel spreadsheet shows the detailed values for the moment capacity using formulas and codes provided by ACI 318-19. From the tabulated moment capacities in the devised excel spreadsheet, we can determine the required number of bars for reinforcement. We will only use the most conservative values as the placement of the bars will vary and change during construction.
Yield Line Method
Type I - Outer Slabs
The yield line method is another method for determining the required number of steel reinforcing bars needed for the slab and the girders. The calculations for the Yield Line method to determine the nominal moment capacity required was done with an Excel spreadsheet. For the outer slabs, the dimensions for where the yield lines occur will be different than the ones in the central slab. The optimal dimensions for determining the minimum required nominal moment was calculated using and Excel spreadsheet. The Yield line method requires the calculation of the external and internal work and setting them equal. We use this to determine the minimum moment capacity that the slab will take per unit length; the unit length in this case will be set as 1 ft.
Type II - Central Slab
The central slab is similar in steps on how to solve for the minimum required moment capacity. The same procedures will be carried out as the outer slabs to determine the nominal moment capacity; the only difference is that the central yield line will coincide with the horizontal center line.
Structural Analysis - Girders
Analysis of All Girders
The girders were initially analyzed using normal area loads of triangles, uniformly distributed, and trapezoidal loads; this is known as assigning each girder to their tributary area. Because of this reason of different load cases, the girders were analyzed into 4 cases individually. Structural-Analyzer.com was also used to determine the governing moments and shears for the girder for each of their cases. The governing bending moments and shears were tabulated into an Excel spreadsheet to later calculate the required amount of reinforcing steel. The moment diagram is seen to the left most image and the shear diagram to the right of it.
Structural Design
Slab Design
This design shows that the bars will be identical throughout all slabs. This design choice is to maintain construct-ability and continuity of the reinforcement bars.
Flexure - Vertical Reinforcement
Top Reinforcement: #4 @ 6” [13.43 k-ft/ft]
Bottom Reinforcement: #4 @ 12” [6.85 k-ft/ft]
Flexure - Horizontal Reinforcement
Top Reinforcement: #4 @ 6” [14.33 k-ft/ft]
Bottom Reinforcement: #4 @ 12” [7.30 k-ft/ft]
Shear Design
The calculations performed for shear in Excel shows that no shear reinforcement is needed for the slab because the concrete shear is sufficient.
Girder Design
Flexure Design
The required flexure reinforcement values were determined using an Excel spreadsheet. The reinforcement types for the girders turned out to be 4 #5 bars for top and bottom reinforcement in G1, G4, and GB; 4 #7 bars for top and bottom in G2 and G3; 4 #6 bars for top and bottom in GA. So, [𝜙𝑀n] ≥ [𝑀u ]; the nominal moment capacity is greater than the greatest absolute moment determined by the structural analysis solver in all cases. This shows that the design is safe enough to withstand its demand.
Shear Design
The required shear reinforcement was calculated in Excel. The design confirmed that the nominal design shear exceeded the demand shear value. The design shear reinforcement was also based off the design of temperature and shrinkage steel.
AutoCAD Design Drawings
The following design has met the serviceability requirements by checking and confirming that the design capacity was greater than the factored loads applied to structure. The reinforcement bars were designed to be continuous to make the drawings understandable during construction, although, it might cost more for steel reinforcement material. This choice is similar to deciding the overall slab thickness to be the same as the minimum cantilever thickness.
Conclusions
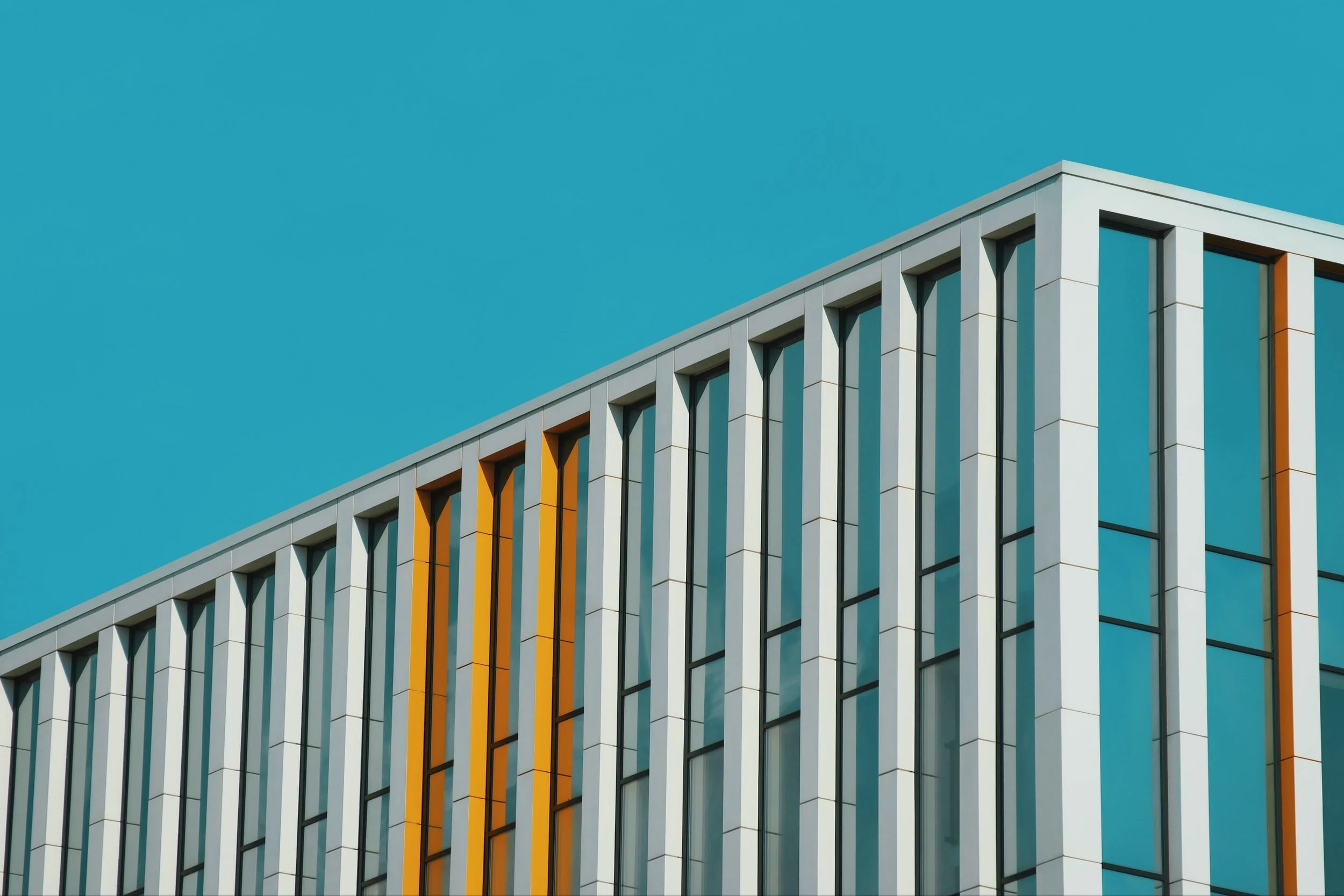